HOW DO VEHICLE EXHAUST EXTRACTION SYSTEMS WORK? A COMPLETE TECHNICAL GUIDE
Vehicle exhaust extraction systems are critical safety installations that protect workers from exposure to deadly carbon monoxide (CO) and other harmful emissions in enclosed spaces. According to the Occupational Safety and Health Administration (OSHA), CO from vehicle exhaust can quickly accumulate to dangerous levels indoors, even in short exposure periods.
These systems are essential in any facility where vehicles operate indoors, from small repair shops to large fleet maintenance facilities, as ventilation alone is not sufficient to maintain safe working conditions.
With vehicles producing exhaust temperatures up to 600°F, these systems must be carefully engineered to handle both the heat and toxic components of vehicle emissions. Modern exhaust extraction systems incorporate components and controls to ensure consistent, reliable operation while meeting all local, state, and federal clean air standards.
Core Operating Principles of Exhaust Extraction
Vehicle exhaust extraction systems operate through a four-phase process that ensures complete capture and removal of harmful emissions. The system's success depends on proper integration of all components, from tailpipe adapters to discharge stacks.
Here's how each phase works:
1. Capture Phase
The system begins at the point of capture, using specialized tailpipe adapters that must be properly sized and selected based on the specific application.
This critical connection point requires careful consideration of both safety and functionality:
• Tailpipe adapters create an at-source capture method and allow necessary ambient air intake to maintain proper system cooling
• Temperature-resistant rubber or silicone adapters rated for up to 600°F, with metal adapters used for high-temperature and vertical exhausts
• Quick-release mechanisms utilizing hook and chain assemblies for secure vehicle attachment
• Automatic disconnection systems requiring the adapter to be 1/2" larger than the tailpipe to prevent temperature issues and hose damage
2. Collection and Transport Phase
Once captured, the exhaust gases move through the immediate collection system, which can be configured in several ways depending on the facility's needs:
• Primary collection occurs through flexible hoses or vehicle exhaust ducting, available in sizes from 4" to 16" diameter
• Negative pressure ensures consistent gas flow, maintained through either direct-mount fans or central blower systems
• Temperature-resistant materials handle hot exhaust gases, with options ranging from 400°F to 2010°F capability
• Variable diameter options accommodate different vehicle types, with specific configurations for both horizontal and vertical exhaust systems
3. Discharge Phase
The final phase safely expels filtered air outside through carefully engineered discharge points:
• High-efficiency exhaust removal extracts particulates before release into the environment
• Stack design ensures proper dispersion of exhaust gases away from the building
• Monitoring systems verify air quality to maintain compliance with environmental regulations
• Weather protection prevents backdraft while maintaining system efficiency in all conditions
Exhaust Extraction System Components in Detail
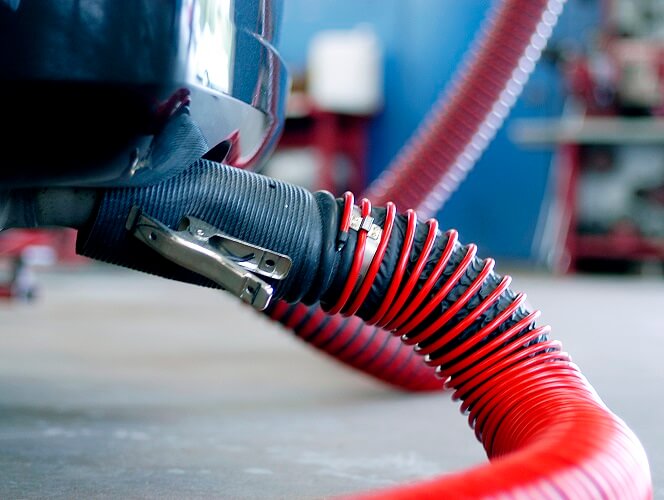
Tailpipe Adapters/Nozzles
• Hook and chain assembly for secure vehicle attachment
• Metal adapters for high-temperature and vertical exhausts
• Rubber adapters for low-temperature undercarriage exhausts
• Sizes ranging from 4" to 16" diameter
• Optional spring clamps and plugs for system control
• Temperature resistance up to 600°F
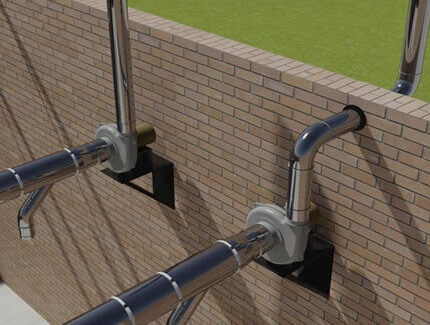
Fan Exhaust Systems
• PB Series Fans with 3/16" minimum thickness radial flat wheels
• Hose Reel Mount Fans with cast aluminum construction
• Direct drive systems with 3450 RPM operation
• Power options from 1HP to 25HP
• AMCA Type B spark resistant design
• Multiple mounting configurations (bottom, horizontal, blast discharge)
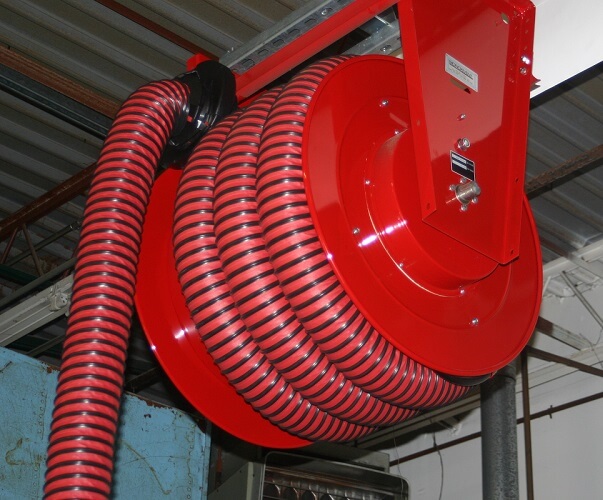
Hose Storage Systems
• Light Duty reels for basic applications
• Spring Operated reels with manual retraction
• Motorized reels with remote control options
• Specialty & Oversized reels for large diameter hoses
• Overhead simple drop systems with rope and pulley
• Spring cable balancer systems for heavier applications
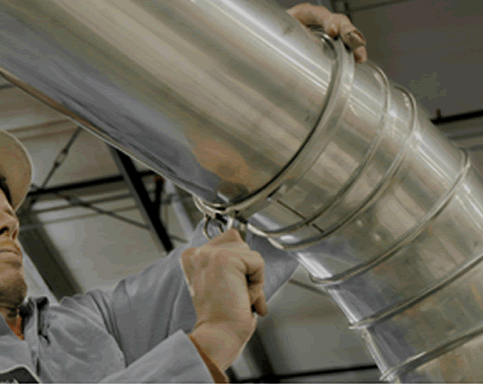
Ducting System
• Self-sealing round duct system requiring no welding
• Base option with simple slip-fit connections
• Premium option with engineered high-performance design
• Specialized sizing different from HVAC ducting
• Tight-fitting seals for maximum efficiency
• Custom CAD-designed layouts for optimal performance
Airflow Calculations
The system operates based on precise airflow calculations:
Required CFM = (Vehicle Exhaust Output) × (Number of Vehicles) × (Diversity Factor)
Typical airflow requirements:
Passenger vehicles: 300-500 CFM
Light trucks: 500-800 CFM
Heavy-duty vehicles: 800-1200 CFM
System Types and Configurations
Overhead Exhaust Systems
• Simple drop systems for cost-effective installation
Two lifting configuration options: Rope & Pulley Systems Spring Cable Balancer Systems
|
Hose Reel Systems
Light Duty Configuration Spring Operated Configuration Motorized Configuration Specialty & Oversized Configuration |
Installation Options
Mounting Configurations
Ceiling Mount Installation Drop Ceiling Mount Wall Mount Installation |
Fan Integration
Direct Mount Configuration Central System Configuration
|
Implementing an effective vehicle exhaust removal system requires careful consideration of multiple factors, from facility layout to specific vehicle types serviced. The choice between overhead systems, hose reels, or specialized configurations depends on workspace constraints, usage patterns, and maintenance requirements.
Each component, from tailpipe adapters to ducting systems, must be properly sized and matched to create a cohesive system that operates efficiently and reliably.
Success in vehicle exhaust removal lies in the details - ensuring proper adapter sizing with the recommended 1/2" larger diameter than the tailpipe, selecting appropriate temperature-rated materials for different applications, and implementing the right mounting solutions for your space.
Whether utilizing simple drop systems for basic needs or advanced motorized reels for specialized applications, the goal remains the same: creating a safer working environment through effective exhaust capture and removal.
The return on investment for these systems extends beyond regulatory compliance. By creating cleaner air conditions, facilities can expect improved worker productivity, reduced maintenance costs, and longer equipment life spans. As automotive technology continues to advance, the ability to adapt and maintain proper exhaust removal systems remains crucial for any professional automotive facility.
Through proper system design, installation, and maintenance, exhaust extraction systems provide the foundation for a safer, more efficient workplace that protects both workers and equipment.
You may also like:
• Vehicle Exhaust Extraction Systems for Commercial Facilities
• Common Misconceptions About Vehicle Exhaust Extraction
• Diesel Exhaust Removal Systems: Safety Solutions for Workspace